How to Use Patterns to Identify Process Safety Hazards
A baby is constantly exploring new things and looking for familiar shapes, colors, and other patterns to help him or her understand the world around them. They are constantly experiencing brand new objects, which their brains must fit into an ever-expanding repository of categories. Sometimes the categorization starts as “not a circle” until they create a new category of “it’s a square!”
One of the ways that we learn new things is to try to categorize a new idea or image with others that we already know.
Patterns in Process Safety
Patterns and trends – defining something by what it IS and ISN’T – help us identify hazards in the workplace.
And sometimes the way to recognize a hazard is by first categorizing it as “not safe.”
I’ve been told that one way to recognize counterfeit money is to be intimately familiar with real money. Then any anomaly stands out and is identified as “not real.”
What if we approached process safety the same way?
What if we learn the procedures for our safe work practices so well that when something is different, it stands out as “not a circle?”
And once I recognize the deviation, I also need to know the reasoning behind the procedure well enough to understand possible consequences!
Ripple Effects of Deviations
Let’s take an example from the steps of Management of Change. Most MOC procedures require a relief systems expert to review each process change. But consider if the change is a simple trim on a control valve which doesn’t seem connected to the relief valve downstream at all.
It might be tempting to skip the relief system review step, but in an emergency, that change would send more material to the relief valve than it can handle. In this case, failing to identify the risk due to a presumption of understanding could have serious consequences.
Owning Your Role in Identifying Hazards
As we said, the best way to identify deviations and hazards, is to be intimately familiar with the processes and procedures so that when something is “off”, you notice it.
You can’t notice when something isn’t right if you don’t know what it should be.
If there’s an item in a procedure that doesn’t make sense, find someone to explain it to you. Bettering your understanding will increase your ownership of the procedure and ensure you don’t miss critical steps because you didn’t realize they were critical.
Looking for deviations is a common way for operating a process unit.
Consider safe operating limits. Alarms go off when the process variable (temperature, pressure, flow) exceeds or falls below a certain safe range.
When you take the time to study the procedures and standards, it allows for an internal alarm to sound in your brain because something isn’t fitting the pattern. “Wait a minute, this P&ID doesn’t match what is in the field…” or “shouldn’t there be a plug on this bleeder?”
What Does “Safe” Looks Like?
At one company I worked for, we often asked the question “What does good look like?”
I challenge each of us as we go about our work to ask the question, “What does SAFE look like?”
When safe designs, procedures, and standards become the patterns you are most familiar with, you can quickly see the outliers and address the hazards.
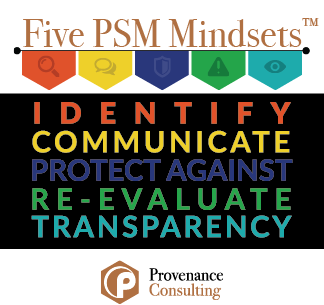
Read More from the Five PSM Mindsets™ Series:
- Identify: How to Use Patterns to Identify Process Safety Hazards
- Communicate: Can Your Hear Me Yet? How to Communicate Hazards Better
- Protect: How to Protect Your Ship from Process Safety Hazards
- Re-Evaluate: How Better Access to PHA Data Can Inform Your MOC Process
- Transparency: How Telling Stories Creates Hazard Transparency